Alesatrice per tunnel
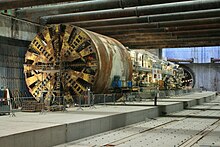
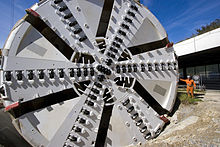
Una fresatrice per tunnel ( TBM ) è una macchina che viene utilizzata per costruire gallerie . È particolarmente adatto per l'hard rock . Macchine così grandi sono utilizzate anche nella costruzione di tunnel in roccia sciolta, che non è adatta per l'azionamento mediante tecnologia di granigliatura . Le perforatrici per gallerie appartengono, insieme alle macchine a scudo (SM), alle macchine per la perforazione di gallerie ( TBM ).
Struttura e tipologie
La parte più importante di una TBM è la testa di perforazione ; ha un diametro fino a 20 metri ed è costituito da un porta scalpello con scalpelli a rulli rotanti , che trasporta all'indietro la roccia scavata. Il dispositivo nella parte posteriore della testa di perforazione ha una lunghezza fino a 200 metri con dispositivi ausiliari per grandi diametri.
Le fresatrici per tunnel sono testate complete , il che significa che, a differenza delle testate parziali , tagliano l'intera sezione del tunnel in un'unica fase di lavoro.
Tali macchine sono solitamente supportate da nastri trasportatori per rimuovere rapidamente il sovraccarico che si verifica durante il lavoro, oppure trasportano con sé un treno di costruzione , ad esempio per portare parti prefabbricate in calcestruzzo per il tunnel da costruire successivamente alla macchina di rivestimento del tunnel similmente tracciante - è possibile anche il calcestruzzo proiettato , che può essere portato alle pareti del tunnel tramite nastri trasportatori o autobetoniere .
Componenti di una fresa per tunnel
- Segnale di smontaggio con scalpelli a rullo, dispositivi di alimentazione e tensionamento
- Strutture per l'installazione di misure di supporto e di espansione
- Attrezzature per asportazione di materiale (sistemi di taglio)
- Unità di alimentazione per elettricità e aria compressa per azionare le punte a rullo, nonché ventilazione e acqua per raffreddare le punte
- Attrezzature per il trasporto di materiale di scavo, materiali di supporto e materiali di finitura
Classificazione delle fresatrici per gallerie tunnel
Una si suddivide in perforatrici aperte ( macchine a pinza aperta e macchine a doppia pinza aperta) e macchine a scudo (macchine a scudo singolo e macchine a doppio scudo , anche macchine a scudo telescopico).
- Le perforatrici per tunnel aperte sono adatte per la guida in roccia stabile e sono utilizzate in vari modi per lo scavo di gallerie di traffico (ferrovie e strade), gallerie di tubi (elettricità, acqua, gas), gallerie d'acqua in pressione (centrali idroelettriche), nonché gallerie per indagini geologiche o funicolari in alta montagna. I componenti principali della fresa a tunnel aperta sono la testa di perforazione con il relativo azionamento, dispositivo di controventatura (rinforzo) e il dispositivo di alimentazione ( Kelly ).
-
Le macchine Shield sono utilizzate per la guida in formazioni rocciose da stabili a non stabili e sono regolarmente utilizzate per guidare gallerie stradali (ferrovie e strade) e gallerie di linea (elettricità, acqua, gas). Il componente che dà il nome a queste trivelle è lo scudo o la guaina dello scudo . Si tratta di strutture tubolari in acciaio in cui sono annegati tutti gli altri componenti della macchina nonché gli spazi di movimento per materiale e personale. Queste parti sono la testa di perforazione con azionamento, la meccanica di propulsione e il dispositivo simile a un robot per l'installazione del rivestimento del tunnel, il cosiddetto erettore. Il rivestimento della galleria, costituito per la maggior parte da elementi prefabbricati in calcestruzzo, viene installato con l'erettore sotto la protezione della camicia dello scudo posteriore, la cosiddetta coda dello scudo.
- Le
- Le TBM a doppio scudo o a scudo telescopico sono infatti una combinazione di una TBM aperta e una a scudo singolo, con l'alimentatore e l'erettore situati nel guscio dello scudo posteriore interno, sul quale può essere spostato un guscio dello scudo anteriore esterno che racchiude l'unità di perforazione assialmente in modo telescopico. Ciò consente di ottenere un alto tasso di anticipo.
Fasi di lavoro nel tunneling
La perforazione avviene in più fasi:
- l'anticipo vero e proprio, in cui una ruota di taglio rotante scava la faccia sotto pressione ,
- la costruzione ad anello in cui dopo il completamento della guida della tubazione con un erettore che riveste l'Ausbruchslaibung e la tenuta. Quindi il trapano si preme tra gli anelli per l'ancoraggio e si spinge nuovamente in avanti.
- Con il New Austrian Tunneling Method (NÖT), l'uso di segmenti non è necessario; Il principale elemento di supporto è la catena montuosa stabile circostante. Come mezzi di fissaggio aggiuntivi vengono utilizzati calcestruzzo armato, ancoraggi per roccia e tralicci.
Con l'ausilio di un sistema a schiuma che genera schiuma con tensioattivi e acqua in pressione, il fronte può essere solidificato nel sottosuolo morbido in modo tale da poter perforare terreni sabbiosi e terreni argillosi. In terreni fangosi, l'ambiente è congelato con azoto liquido (congelamento del suolo ).
Uso singolo o riutilizzo
Le perforatrici per gallerie di solito lasciano dietro di sé una galleria parzialmente completata con una sezione trasversale inferiore al diametro di scavo e al diametro dello scudo della macchina. Ciò è dovuto a segmenti, ancoraggi sporgenti per perforatrici da roccia, rivestimenti di gallerie e dispositivi come la carreggiata, i tubi di drenaggio e di ventilazione. Ciò significa che una TBM può avanzare solo in una direzione e non può essere retratta. L'operatore deve quindi mantenere un certo margine di manovra per ritirare lo scudo nel caso in cui singole parti si guastino o si intasino con rocce in modo che alcune parti possano essere sostituite o scomposte. Il dispendio di tempo e materiale per le riparazioni è elevato a causa della limitata accessibilità e dell'approvvigionamento di ricambi.
Se le gallerie vengono affrontate solo da un lato, ovvero perforate in una direzione, la macchina si trova nuovamente sulla superficie o in prossimità di essa quando la galleria si sfonda e, a condizione che le dimensioni lo consentano, può essere trasportata nel sito successivo. Se la macchina, più o meno smontata in più parti, viene capovolta e spostata un po', può essere utilizzata per costruire un secondo tubo parallelo.
Via terra - strada o ferrovia - le TBM di grandi dimensioni possono essere trasportate solo smontate. Anche lo scudo deve poter essere smontato. Esistono navi con una stiva sufficientemente grande, ma solo in rari casi è possibile portare una TBM direttamente sul luogo di utilizzo via acqua.
Se - tipicamente per lunghe - gallerie ci si avvicina da due lati o anche da più punti, una TBM deve inevitabilmente essere smontata in montagna. Questo può essere fatto con l'intenzione di rimontare rapidamente una macchina funzionante con queste ed eventualmente nuove parti; per l'uso nelle vicinanze o altrove. Se non è prevedibile la necessità di una macchina di questo tipo, alcune parti vengono conservate e smontate per il riutilizzo e il telaio della macchina smontato e rottamato.
Nella lista delle più grandi perforatrici (sotto) ci sono esempi di riutilizzo delle TBM su grandi distanze geografiche: Paesi Bassi – Cina, Germania – Russia.
Aziende manifatturiere e storia
Nel 1844, l'ingegnere scozzese e inventore fu William Brunton (* 26. Maggio 1777 a Dalkeith , † 5. Ottobre 1851 a Neath (Galles) ) con l'idea di una costruzione di un tunnel tra Inghilterra e Francia Hammer da aria compressa per la spinta di e perforazione per azionare; i compressori necessari non erano ancora stati sviluppati a questo punto. La sua macchina era come un gigantesco trapano del diametro del tunnel, che avrebbe dovuto schiacciare la roccia e gettare i frammenti nel pozzo perforato che era stato creato per la rimozione.
Con la perforazione di testa basata sul brevetto Fowler del 1849, la perforazione meccanica iniziò nel 1857 e l'introduzione della perforatrice a percussione ad aria compressa ridusse i tempi di costruzione del tunnel del Moncenisio da 25 a 12 anni.
Sui trapani a percussione , il pistone e l'asta di perforazione sono collegati da un blocco a cuneo. Con una frequenza di corsa da 250 a 300 corse al minuto, lavorano con corse da 50 a 250 mm e con pesi totali fino a 280 kg possono lavorare solo su slitte di bloccaggio con avanzamento a vite a manovella su una colonna di bloccaggio o su treppiede .
Intorno al 1870 ci furono i primi tentativi di utilizzare una fresa per tunnel per una guida più veloce durante la costruzione del tunnel Hoosac sulla costa orientale ( Boston ) degli USA e allo stesso tempo il rischio di lesioni agli operai - dal lavoro con martello e scalpello e sabbiatura con polvere nera (solo più tardi i precursori del martello pneumatico e la nitroglicerina usati qui per la prima volta) - per ridurre. Alla presentazione alla stampa in loco, era finita dopo circa 15 centimetri: si è incastrata. Gli scalpelli in ghisa si sono rivelati troppo morbidi e il motore a vapore troppo debole per guidarli.
Nel 1897, J. G. Leyner di Denver sviluppò il trapano a percussione . Funzionava secondo il principio di battitura con spurgo dell'aria, per cui il pistone colpisce l'estremità di inserimento del trapano con solo 1/10 del suo peso a 1500 battiti al minuto e un mandrino a rotazione con nottolini sposta il trapano da 12 a 45 gradi per battito quando il il pistone cade sul guida punte. Anche questi dispositivi furono inizialmente utilizzati, come i trapani a percussione, su colonne di bloccaggio o treppiedi con slitte di bloccaggio e avanzamento manuale. Dopo il 1918, hanno già raggiunto da 10 a 13 volte le prestazioni dei trapani a percussione, ma con un consumo d'aria più elevato.
L'ulteriore sviluppo di questi trapani a percussione ha portato, con la sostituzione del riduttore ad ingranaggi nel 1955, ad un azionamento a pressione e infine ad un azionamento a motore idraulico con una coppia elevata e costante.
L'ulteriore sviluppo basato sulle idee di Brunton nella costruzione di gallerie e gallerie, che è sempre più utilizzato nella costruzione di ferrovie sotterranee quando le condizioni del terreno sono adatte, è caratterizzato dall'uso di macchine per la guida di gallerie o gallerie per diametri fino a 10,5 metri. L'idea è stata ripresa negli anni '60 e inizialmente utilizzata solo nelle miniere e poi nei trasferimenti sotterranei. Lug e le macchine scava-tunnel rappresentano il vuoto sotterraneo senza il ciclo di lavoro intermittente di perforazione, sabbiatura, caricamento e convogliamento in continuo avanti utilizzando strumenti adatti alla montagna in arrivo, mediante lavorazioni a 11,7 kN / cm² con rulli scalpellatori o taglienti per 21,6 kN/cm² attaccano il seno e rilasciano continuamente il materiale degradato dietro di essi. Sono stati costruiti negli Stati Uniti dal 1950 in un'ampia varietà di forme. I vantaggi risiedono nell'evitare l'allentamento eliminando la sabbiatura, riducendo il profilo eccessivo e richiedendo meno personale. Gli svantaggi sono gli elevati costi di investimento e i costi di gestione dell'usura degli utensili. Sono diventate note le macchine per ancoraggio pilota Alkirk-Lawrence e l' Oil-Shaleminer , che guidano in anticipo un'ancora pilota, su cui la testa di perforazione tira contro il petto. La Robbins Company utilizza macchine dall'inizio degli anni '60 , nelle quali i frammenti di perforazione che erano stati staccati dal taglio della testa di fresatura vengono prelevati da benne o benne da escavatore e versati sul nastro di scarico in corrispondenza dell'apice. Gli sviluppi inglesi e giapponesi delle macchine per la perforazione dello scudo funzionano all'interno di uno scudo per il tunneling supportato dall'estensione, con una grande testa di fresatura che circonda l'intera faccia o, presso Mitsubishi Heavy Industries, con quattro teste di fresatura rotanti in direzioni opposte. In Germania, sono state le macchine di Demag , Wirth e Atlas Copco e le macchine per la guida di scudi di Bade-Holzmann che hanno aperto la strada alla costruzione di gallerie e gallerie negli anni '60. Nel frattempo, nella Repubblica Federale Tedesca sono state sviluppate macchine scavatrici completamente meccaniche adatte alla costruzione di gallerie inclinate, per la costruzione di pozzi verticali e per l'espansione graduale delle sezioni trasversali fino a 11 m. Per resistenze della roccia di 20 kN / cm², vengono utilizzate frese per verruche, denti e dischi.
Dal 1966 le macchine integrali vengono utilizzate per profili da 2 a 6,4 m di diametro, con pesi da 48 a 90 t e lunghezze da 11,5 a 21 metri. A seconda del materiale e del diametro, la loro potenza di azionamento è compresa tra 240 e 950 kW, la velocità della testa di perforazione è compresa tra 12,7 e 5 giri al minuto e la pressione di contatto è fino a 8000 kN. La costruzione delle macchine per tunnel mostra i seguenti componenti:
- la testa di perforazione dotata di punte a rullo da 8 a 10, da 18 a 23 e da 18 a 33,
- il parapolvere con guarnizione in gomma dietro la testa del trapano,
- Raschiatori e pale che alimentano il truciolo tramite uno scivolo al trasportatore raschiatore a catena singola installato sotto la macchina o un tappeto in gomma concava che li trasferisce alla fine ad un nastro di carico ascendente,
- da due a quattro motori elettrici con una potenza totale da 240 a 950 kW, che forniscono l'azionamento tramite alberi cardanici, ingranaggi e frizioni,
- un sistema idraulico per controventare, spingere in avanti e sostenere.
La macchina è trattenuta nel tubo del tunnel per mezzo di artigli mediante controventatura anteriore e posteriore con almeno 130 N/cm². La pressione di contatto della testa di perforazione è da 1600 kN a 2 m a 6400 kN a 6 m di diametro. Le trivelle sono controllate da una stazione di controllo nel tender; possono essere torniti con un raggio di 80 m per un diametro di 2,4 me un raggio di 150 m per un diametro di 6 m; un laser viene utilizzato per il controllo fiscale. Il primo dispositivo è stato utilizzato nel 1966 per la realizzazione di un tunnel fognario lungo 2800 m in arenaria verde con un diametro di 2,1 m a Dortmund; il dispositivo di 6 metri è stato utilizzato nel 1973 sul Basso Reno.
La quarta canna del tunnel dell'Elba ad Amburgo è stata costruita tra il 1997 e il 2000 utilizzando la macchina per gallerie a scudo TRUDE, che pesa 2.000 tonnellate e ha un diametro esterno di 14,20 m. La più grande fresatrice per tunnel del mondo in quel momento allungava il tunnel in media di 6 m / giorno con 111 coltelli da taglio per roccia tenera e 31 punte a rullo per roccia dura. Il disco da taglio con la "tecnologia Mixshield" è stato sviluppato dalla ditta Herrenknecht di Schwanau . Caratteristici erano i cinque raggi accessibili per la prima volta dall'interno per il cambio degli utensili da taglio e una fresa centrale controllabile indipendentemente.
In Svizzera, negli anni '60, i profili più piccoli sono stati inizialmente prodotti con macchine per la perforazione di tunnel. Dal 1970 sono state scavate anche grandi gallerie per il traffico stradale e ferroviario con macchine perforatrici. Alla fine degli anni '90, 19 grandi gallerie stradali o ferroviarie a doppia corsia con una lunghezza totale di 83 km erano state realizzate con le TBM. La galleria di base del San Gottardo è stata realizzata tra il 2002 e il 2010 con le perforatrici per tunnel Heidi (S - 211) e Sissi (S - 210) della Herrenknecht AG, lunghe 400 m e pesanti 2700 t . Le teste di perforazione delle macchine avevano un diametro di circa 9,5 me erano dotate di oltre 60 punte a rullo. Erano azionati da dieci motori da 350 kW ciascuno.
La testa di perforazione come con l'azionamento all'estremità anteriore del dispositivo di alimentazione, in gergo tecnico Kelly è chiamata colpita (la Kelly era nel petrolio perforando un alloggiamento fissato all'albero di perforazione abbassato sezione superiore del tubo di sezione poligonale (come un chiave a brugola sovradimensionata ) che guidava e ruotava una tavola rotante con questa stessa apertura poligonale, il tubo poteva essere abbassato nella guida della tavola di foratura con profondità di foratura crescente). Il dispositivo di alimentazione è costituito da una parte interna, alla quale è fissata la testa di perforazione, il kelly interno, e una parte esterna, il cosiddetto kelly esterno. Il kelly esterno della macchina è fissato nel tubo del tunnel perforato per mezzo del rinforzo. Il kelly interno con la testa di perforazione fissata all'estremità anteriore scorre durante il processo di foratura parallelamente alla direzione di foratura nel kelly esterno nella direzione di foratura in avanti. Il kelly interno e il kelly esterno sono collegati tra loro tramite il cilindro di alimentazione. I cilindri di alimentazione spingono in avanti il tamburo interno insieme alla testa di perforazione. La testa del trapano della macchina è dotata di rulli di taglio, che sono dotati di anelli di metallo duro e sono chiamati rulli di taglio del disco. L'azionamento rotante della testa di perforazione è dotato di motori idraulici o motori elettrici, per cui la variante di azionamento elettrico è diventata la più comune al giorno d'oggi. Il controllo continuo della velocità della testa di perforazione è diventato nel frattempo uno standard nelle moderne perforatrici per tunnel. Attorno alla testa di perforazione della macchina, l'involucro della testa di perforazione, è disposto uno schermo in acciaio che da un lato svolge una funzione di supporto per il tubo del tunnel perforato e dall'altro funge da protezione della testa contro la caduta di rocce. La roccia scavata viene trasportata via su nastri trasportatori e caricata in vagoni per il trasporto fuori dal tunnel o trasportata fuori dal tunnel tramite nastro trasportatore. Immediatamente dopo il processo di perforazione, il tunnel perforato viene supportato con il cosiddetto sistema di fissaggio iniziale, se necessario. Questo fissaggio iniziale può essere costituito da ancoraggi da roccia pesanti, archi di sostegno in acciaio e/o tappetini in acciaio, a seconda delle esigenze. Viene utilizzato anche il calcestruzzo proiettato. Il prolungamento finale del tubo del tunnel trivellato verrà portato dietro la macchina in un secondo momento e seguirà la fresatrice.
Sono poche le aziende al mondo che producono queste macchine. In Germania si tratta delle società Herrenknecht AG di Schwanau e Aker Solutions (ex Aker Wirth GmbH) di Erkelenz ; la Robbins Company negli Stati Uniti, Mitsubishi , IHI , Kawasaki e Hitachi Zosen in Giappone sono altri produttori. NFM Technologies SA in Francia costruita con le licenze di MHI ( Mitsubishi Heavy Industries ) e successivamente SHMG (Shenyang Heavy Machinery Group). L'ex produttore canadese Lovat è stato acquistato da Caterpillar nel 2008 e chiuso nel 2013.
Herrenknecht stima il mercato globale delle macchine per la costruzione di tunnel a circa 1,5 miliardi di euro, di cui la società afferma di coprire circa 1,1 miliardi di euro (dal 2014).
Con i trapani ad ultrasuoni ( "perforazione ad ultrasuoni" ) è possibile una guida più veloce di Fräsbohrern. Il BADGER (robot per la costruzione di tunnel) è un progetto di ricerca finanziato dall'UE per creare un robot di perforazione della terra che lavora in modo autonomo che produce le pareti del tunnel come una stampante 3D in cemento . BADGER è un apronym per "ro B ot per una utonomous un D er G trenchless rotonda op ER zioni, la mappatura e la navigazione".
Progetti famosi
Di seguito è riportato un elenco di progetti di tunnel che sono stati realizzati con macchine perforatrici o sono ancora in costruzione:
Germania
- Tunnel Albvorland ( nuova linea Wendlingen – Ulm )
- Boßler Tunnel ( nuova linea Wendlingen – Ulm )
- City-Tunnel Lipsia (tunnel della linea principale per la S-Bahn nella Germania centrale, Lipsia)
- Filder Tunnel (progetto ferroviario di Stoccarda 21 )
- Finne Tunnel ( nuova linea Erfurt – Lipsia / Halle )
- Kaiser Wilhelm Tunnel (seconda canna tra Ediger-Eller e Cochem)
- Galleria Katzenberg (collegamento ferroviario Karlsruhe – Basilea)
- Soluzione combinata (Karlsruhe) ( metropolitana di Karlsruhe )
- Nuovo tunnel Schlüchtern (secondo tunnel sotto il prato di cardi vicino a Schlüchtern)
- Metropolitana leggera nord-sud (Colonia)
- TRUDE (autostrada A7, quarta canna del tunnel dell'Elba, Amburgo)
- Tunnel ferrovia a lunga percorrenza nord-sud ( tunnel Tiergarten, Berlino)
- Traforo Rastatt (linea Karlsruhe-Basilea nuova / rinnovata)
- U-Bahn linea 5 (Berlino) (estensione tra Alexanderplatz e la Porta di Brandeburgo, Berlino)
- VERA (linea 4 della metropolitana, Amburgo)
- Sezione di costruzione 40 della fognatura di Emscher (due canne parallele lunghe dieci chilometri tra Bottrop e Oberhausen)
Austria
- Galleria di base del Brennero (parti della via di accesso nord)
- Tunnel Koralm (sezione della ferrovia Koralm)
- Tunnel Pfänder ( canna ovest)
- Galleria di base di Semmering (tratto Fröschnitzgraben)
- Wienerwaldtunnel (collegamento ferroviario)
Svizzera
- Nuova Ferrovia Trasversale Alpina (NEAT):
- Galleria Vereina ( galleria ferroviaria a scartamento metrico con divisione a Y)
- Tunnel Weinberg (tunnel ferroviario, Zurigo)
- Galleria di base Zimmerberg (galleria ferroviaria, Zurigo. 1a tappa)
Altri
- Canale di Navarra (Spagna)
- Citytunnel Malmö (collegamento ferroviario a Malmö, Svezia)
- Eurotunnel (collegamento ferroviario Inghilterra-Francia)
- Tunnel ferroviario del Grande Belt (Danimarca)
- Hallandsåstunnel (linea ferroviaria Göteborg – Lund, Svezia)
- Niagara Tunnel Project ("Big Becky", TBM con 14,4 m di diametro; sfondamento maggio 2011; completamento estate 2013)
- Tunnel di Westerschelden (Paesi Bassi)
- Tunnel Hsuehshan (autostrada nazionale di Taiwan n. 5)
- Crossrail (collegamento ferroviario a Londra)
Elenco delle più grandi perforatrici per tunnel
No. | anno | nazione | tunnel | Produttore / tecnologia | diametro |
---|---|---|---|---|---|
1 | 2015 | Hong Kong | Tuen Mun - Tunnel autostradale Chek Lap Kok | Herrenknecht Mixshield | 17.60 |
2 | 2011 | stati Uniti | Tunnel sostitutivo per l'Alaskan Way Viaduct, Seattle | Scudo Hitachi Zosen EPB | 17.48 |
3 | 2016 | Italia | Galleria Santa Lucia ( A1 ) | Herrenknecht EPB segno | 15.87 |
4° | 2015 | Cina | Tunnel del fiume Yangtze sulla metropolitana di Wuhan | Herrenknecht Mixshield (2 ×) | 15.76 |
5 | 2011 | Italia | Galleria Sparvo ( A1 ) | Herrenknecht EPB segno | 15.55 |
6° | 2011 | Cina | Tunnel del fiume Yangtze occidentale di Shanghai | Herrenknecht Mixshield, ex n. 8 | 15.43 |
7° | 2010 | Cina | Tunnel di Qianjiang, Hangzhou | Herrenknecht Mixshield, ex n. 8 | 15.43 |
8° | 2006 | Cina | Shanghai Changjiang Daqiao | Herrenknecht Mixshield (2 ×) | 15.43 |
9 | 2005 | Spagna | Tunnel autostradale Madrid Calle 30 | Herrenknecht | 15.20 |
Mitsubishi | 15.00 | ||||
10 | 2013 | Italia | Galleria Caltanissetta, Sicilia (SS 640) | Tecnologie NFM | 15.08 |
11 | 2011 | Cina | Tunnel stradale Weisan, Nanchinoj | TBM per liquami IHI / Mitsubishi / CCCC (2 ×) | 14.93 |
12° | 2012 | Cina | Tunnel stradale di Hongmei, Shanghai | Herrenknecht Mixshield | 14.93 |
13 | 2008 | Cina | Tunnel del fiume Yangtze Nanchinoj | Herrenknecht Mixshield (2 ×) | 14.93 |
14° | 2013 | Cina | ? | Herrenknecht Mixshield, ex n. 13 | 14.93 |
15° | 2006 | Cina | Tunnel stradale di Jungong, Shanghai | Tecnologie NFM, ex n. 17 | 14.87 |
16 | 2004 | Cina | Tunnel stradale di Shangzhong, Shanghai | Tecnologie NFM, ex n. 17 | 14.87 |
17° | 2000 | Olanda | Groene Harttunnel (ferrovia) | Tecnologie NFM | 14.87 |
18° | 2006 | Canada | Progetto del tunnel del Niagara | Robbins Hard Rock Gripper TBM | 14.40 |
19° | 2013 | Nuova Zelanda | Waterview Connection, Auckland | Herrenknecht EPB segno | 14.41 |
20 | 2004 | Russia | Tunnel autostradale di Silberwald, Mosca | Herrenknecht Mixshield, ex n. 22 | 14.20 |
21 | 2001 | Russia | Tunnel Lefortovo , Mosca | Herrenknecht Mixshield, ex n. 22 | 14.20 |
22 | 1997 | Germania | 4. Tubo del Nuovo Tunnel dell'Elba | Herrenknecht Mixshield ( TRUDE ) | 14.20 |
23 | 2009 | Cina | Yingbinsan Road Tunnel, Shanghai | Insegna Mitsubishi EPB, ex n. 24 | 14.27 |
24 | 2007 | Cina | Bund Tunnel, Shanghai | Mitsubishi EPB segno | 14.27 |
25 | 2004 | Giappone | Linea Namboku della metropolitana di Tokyo | Segno IHI EPB | 14.18 |
26 | 1994 | Giappone | Tōkyō-wan-Aqua-Line (Trans Tokyo Bay) | 8 TBM: 3 Kawasaki, 3 Mitsubishi, 1 Hitachi, 1 IHI | 14.14 |
27 | 2010 | Spagna | Autostrada SE-40 , Siviglia | Tecnologie NFM (2 ×) | 14.00 |
Guarda anche
link internet
- Spiegazioni della TBM sull'esempio del tunnel cittadino di Lipsia
- Installazione di un anello cieco con l'esempio del tunnel cittadino di Lipsia
- Video: Come funziona una fresa per tunnel a scudo singolo. In: bauforum24.tv , 2011, 3:44 min.
Evidenze individuali
- ↑ Foratrici per gallerie per roccia dura. ( Memento dal 12 febbraio 2013 in archivio web archive.today ) In: Aker Wirth GmbH , si accede il 5 maggio 2015.
- ↑ TBM a scudo singolo - avanzamento rapido in condizioni di montagna variabili. Sito web della Herrenknecht AG, consultato il 14 settembre 2018
- ↑ TBM doppio scudo - Avanzamento continuo alla massima velocità. Sito web di Herrenknecht AG, consultato il 14 settembre 2018
- ^ Journal Over Land and Sea , Tunnel tra Inghilterra e Francia, Deutsche Verlags-Anstalt , Berlino, 1881.
- ↑ Georg Garbotz , Baumaschinen once and now , in: Baumaschine und Bautechnik , Frankfurt am Main, ISSN 0005-6693 , 22° anno, numero 5, 1975, pagine 153 ss.
- ↑ TRUDE - La più grande macchina per tunnel a scudo al mondo. In: Museum der Arbeit , Amburgo, consultato il 5 maggio 2015.
- ↑ Leonhard Schmid, Josef Elmiger: Come è dovuto all'elevata percentuale di macchine che scavano tunnel in Svizzera . In: Tecnologia delle gallerie per compiti futuri in Europa . Balekma-Verlag, Rotterdam 1999, ISBN 90-5809-051-5 , pp. 59-71.
- ↑ Galleria di base del San Gottardo. In: Herrenknecht , marzo 2011, consultato il 5 maggio 2015.
- ↑ TBM a scudo singolo . In: Herrenknecht , consultato il 5 maggio 2015.
- ↑ Max Hägler: "Il tedesco ha davvero paura di tutto" . In: Süddeutsche Zeitung . 20 gennaio 2014, pag. 16 .
- ↑ Hall of Fame della tecnologia mineraria internazionale
- ↑ Cos'è il progetto BADGER?
- ↑ Robot BADGER può perforare tunnel sotterranei e di stampa 3D
- ^ Progetto del tunnel del Niagara. Fatti tecnici. Di: Ontario Power Generation e Strabag , consultato il 5 maggio 2015.
- ↑ Tracciamento delle mega-TBM del mondo , TunnelTalk
- ↑ Chronicle - una storia di successo da oltre 35 anni herrenknecht.com, fino al 2015, accesso 11 dicembre 2016.
- ↑ Trivelle XXL nel delta del fiume YangtzeTunneltrici XXL nel delta del fiume Yangtze , 14 marzo 2014
- ↑ "Per la costruzione della sezione Azabu della linea Azabu della linea Namboku della metropolitana di Tokyo è stata utilizzata la perforatrice a doppia schermatura del diametro di 14,18 m più grande al mondo"
Osservazioni
- ↑ Il termine stabilità descrive la capacità degli strati rocciosi di rimanere in piedi attorno a una cavità sotterranea non supportata per un certo periodo di tempo senza essere distrutti. (Fonte: Walter Bischoff, Heinz Bramann, Westfälische Berggewerkschaftskasse Bochum: Das kleine Bergbaulexikon. )